To further boost the capacity of employees and improve overall service performance, Meridian Port Services Ltd (MPS) has instituted a Lean Employee Training Program. To kickstart the training program, the Management Team of MPS was taken through a 2-day Lean leadership training.
The Chief Executive Officer, Mr. Mohamed Samara who opened the training program, underscored the need for individual and collective self-development for organisational performance.
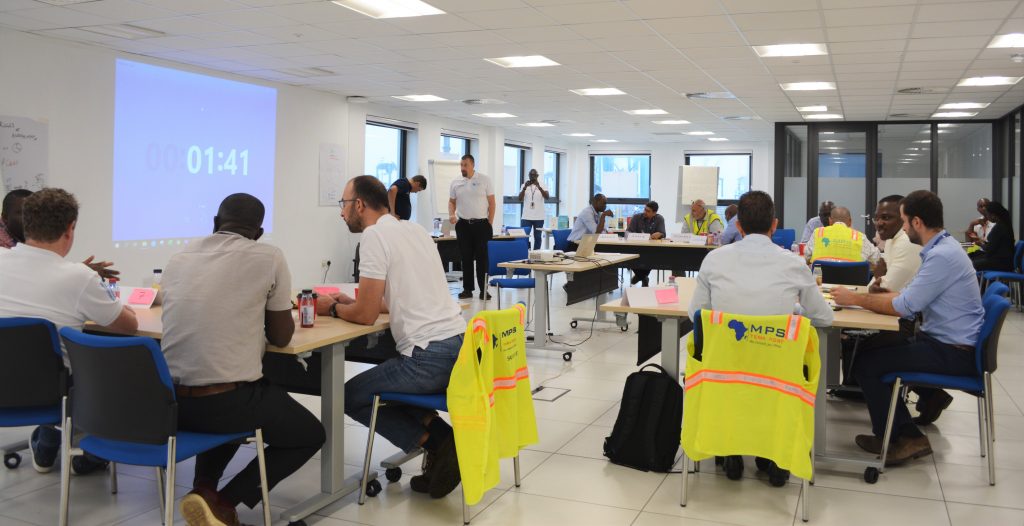
“To further strengthen the gains we have made through the years that have brought significant benefits to MPS and the entire port community, we decided to undertake this Lean training program. Primarily, this program will aim at transforming the way we think and our approach to work. At the end of this, each employee from the highest level of the hierarchy should be able to troubleshoot on their own when faced with problems in the course of their work to arrive at a workable solution”
Again, change starts with leadership, we must recognise that that we exist to deliver top- level service to our customers so we must always seek to add value to our service for the benefit of the customer and ultimately to our advantage as individuals and an organisation. For us as a forward looking terminal, it will help us identify and reduce operational bottlenecks to have a free-flowing process. Mr. Samara added.
Transformational changes of this magnitude are not new to MPS, since the start of operations, MPS has pioneered within the port community long-standing best practices and procedures, HSSE standards as well as innovation in handling machinery, technology and operational processes that have given a global facelift to the Tema Port.
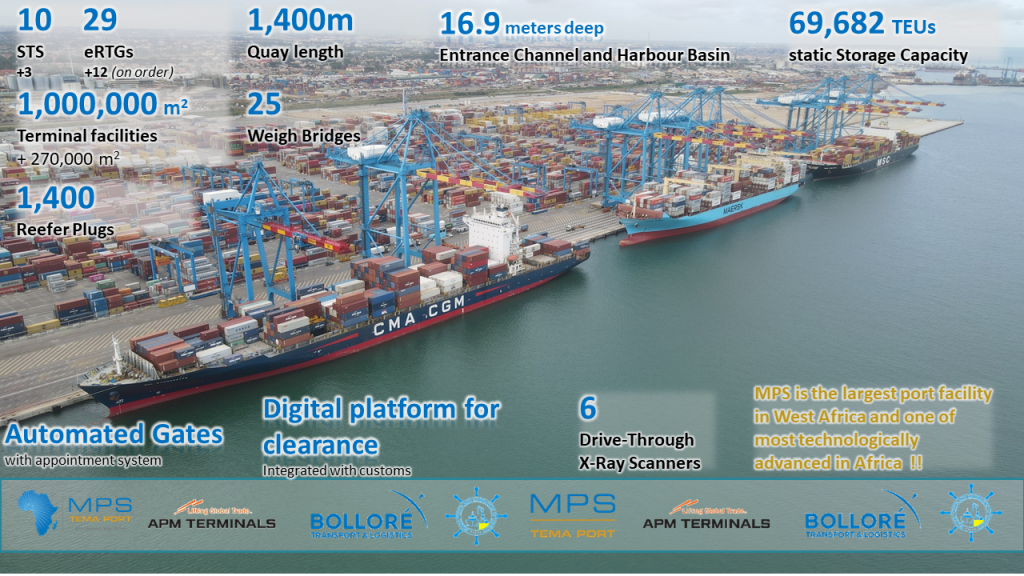
TRAINING
In the 2-day session, Management members went through the basics of Lean Management System, basics of Kaizen, leadership in performance management amongst other Lean related topics and activities.
Over 500 employees of MPS are following up with their training to imbibe the Lean mindset allowing for quick thinking and better approach to problem solving together to eliminate waste, boost productivity and promote innovation.
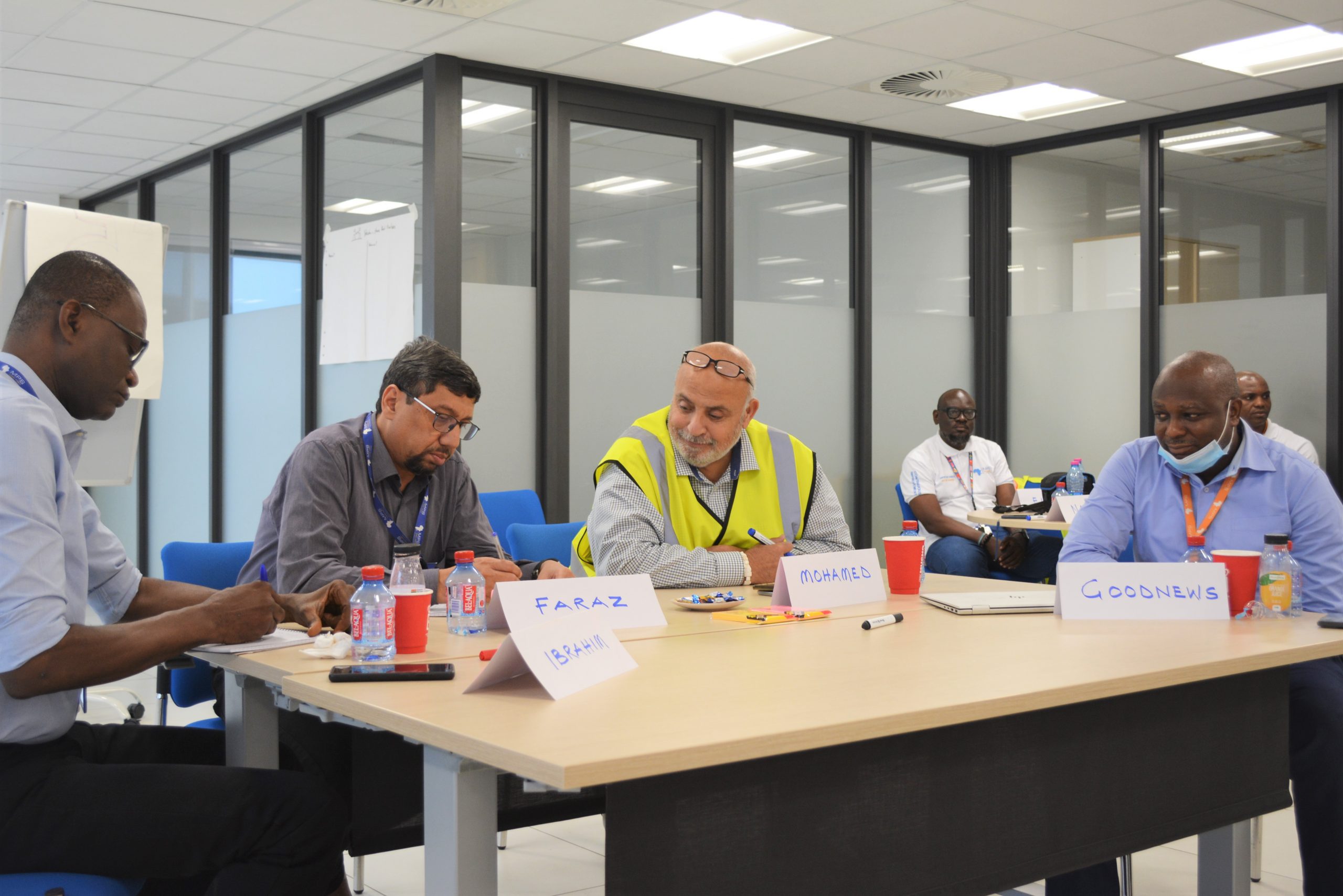

The training was conducted by APMT Lean Trainers Mr. Daniel Berry, Way of Working Regional Lead (AME/ASI Region) and Mr. Sami Palonen, Global Academy Lead.
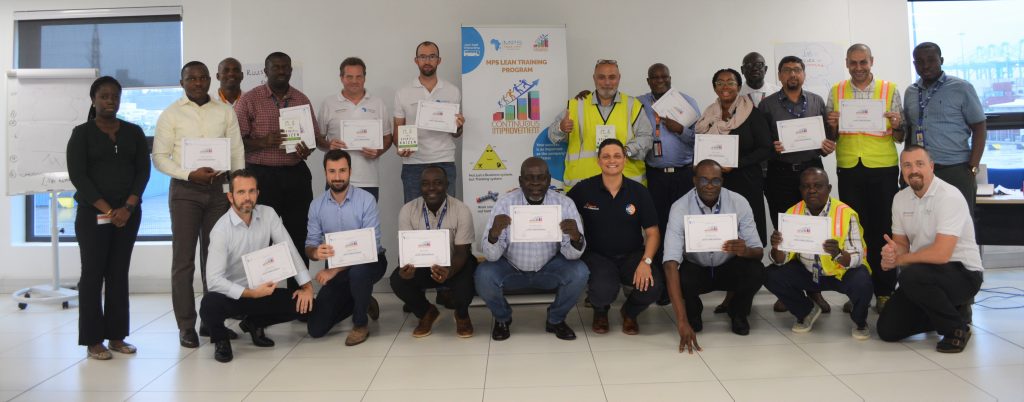
ABOUT LEAN
Founded in the 1950s, Lean thinking is a transformational framework that provides a new way to organising human activities to deliver more benefits to society and value to individuals while eliminating waste.
No Comments