In furtherance of its digitalisation drive and innovative solutions, Meridian Port Services Ltd (MPS) is once again deploying Business Intelligence tools to optimize operational processes by developing inhouse data-driven decision-making intelligence tools. This provides analyses on operations and equipment deployment to monitor performance and productivity.
Jesse Afari, the Data Analyst/ Power BI Developer at MPS who led the development of this tool commented” “this is one of my best works yet” a testament to the enabling environment provided by MPS for growth of its employees.”
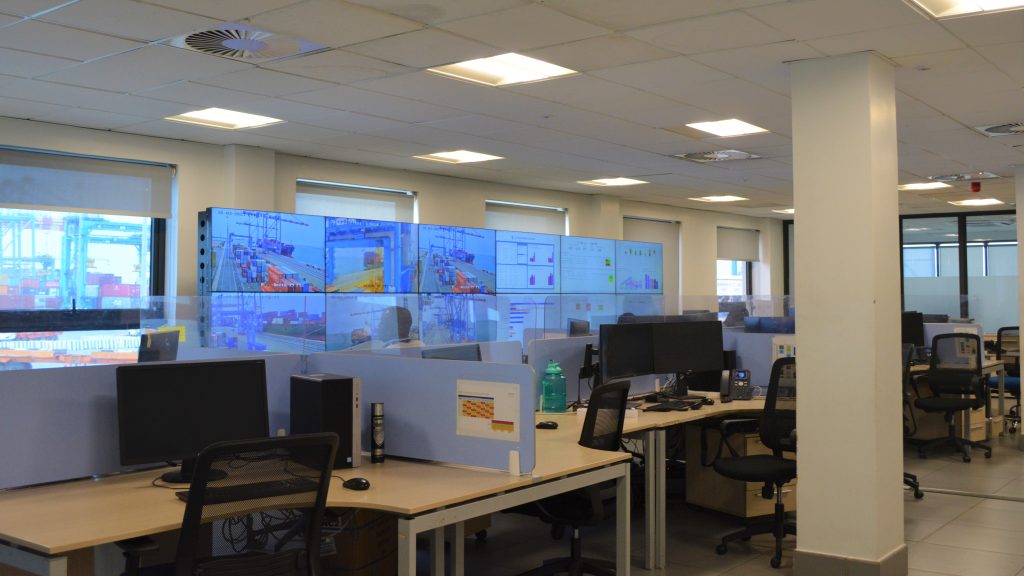
“The dashboard provides a comprehensive view of container handling operations, allowing us to monitor container movement, crane productivity, and identify areas for improvement. This was achieved by first understanding the business logic with the help of the operations team. With dynamic visuals and interactive filters, our team can easily monitor performance and quickly respond to delays and bottlenecks.
The dashboard has metrics color-coded, so immediately, we can easily see whether we are meeting targets or below. Thanks to the ‘Near real-time’ nature of the dashboard, our operation staff can see delays and other issues as they occur, allowing us to take corrective action quickly. This has led to significant time and cost savings, and our team is now able to respond to issues more efficiently. I’m proud of the impact this dashboard has had on our operations”.
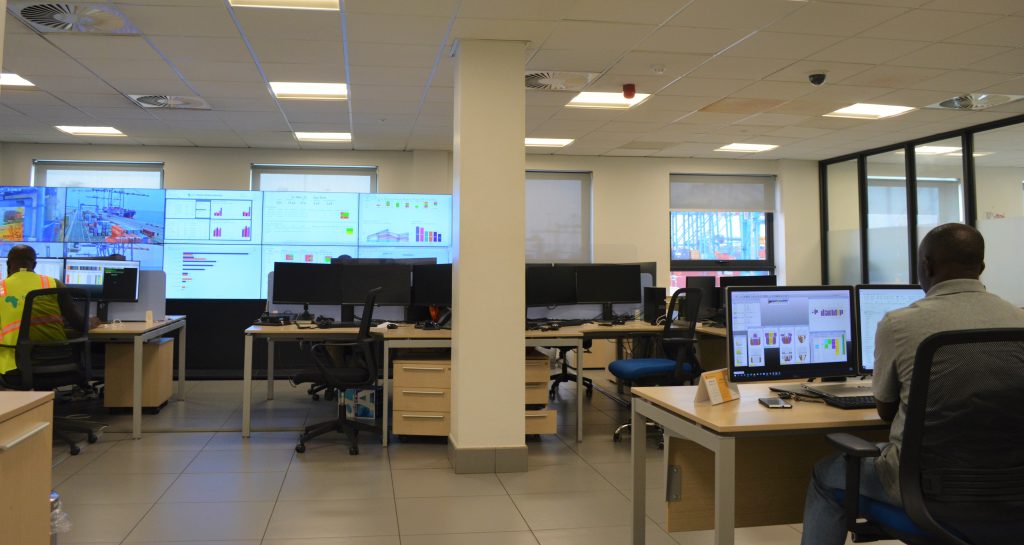
Mr. Bram de Jong (IT Manager) and Mr. Faraz Ahmad (TOS Manager) at MPS who supervised the project commended the work done while detailing the need to keep improving IT solutions for operational excellence.
“This feat has been made possible through the effective collaboration of the Operations and IT Team, particularly brilliant work by Jesse who through perseverance keeps finding ways to improve the data structures and operational dashboards with real-time data updates on vessel, yard, and gate operations. MPS ensures that work is done in line with best industry practices. The operational decisions are made based on data-driven insights from readily available dashboards. This goes a long way to increase customer experience and satisfaction.”
The CEO of MPS, Mr. Mohamed Samara who shared his thoughts on the development remarked “the overall goal of the business is to quickly adapt to change, stay innovative and ahead of the times while determining to increase efficiency in our service provision. In recent times, MPS has adopted a problem-solving environment through its Lean Management Program aimed at significantly advancing its operations on all fronts using continuous improvement tools.”
He added that the dashboard has also been extremely beneficial in improving crane productivity as underperforming cranes are identified for the needed corrective action which translates into efficiency as crane use is optimised.
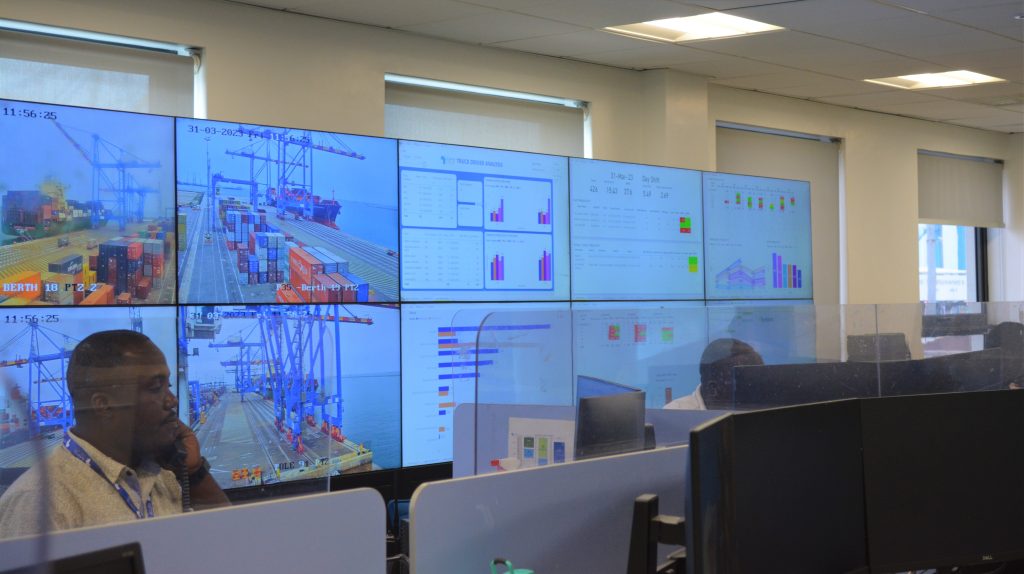
BACKGROUND
One of MPS main commitments to stakeholders is to ensure that it continuously improves services to promote the ease of doing business in our port facility and within the Port Community.
It is within this background that MPS pursued the digitalization drive and successfully implemented the Paperless Port processes. The implementation of the Gate Operation Systems with biometric access controls, the Licence Plate Recognition Systems, the Optical Character Recognition Systems, Import and Export Scanning systems and the real-time updates of containers loaded and offloaded from vessels in the Coarri and Codeco System, have greatly enhanced efficiency, border security and revenue collection at Terminal 3.
To complement this, the Finance System (IFS) has been upgraded to the latest version of IFS 10 from the Legacy 7.5 version in line with global standards.

~END~
No Comments