Meridian Port Services Ltd (MPS) has since the introduction of the Employee Lean Training Program in 2022 executed a successful Kaizen event.
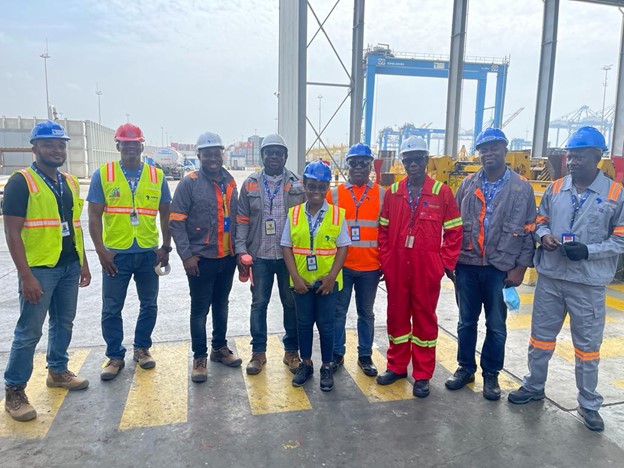
This was undertaken by the first batch of Lean level 3.1 graduates. As part of the training at the level 3.1, the batch were expected to utilise the 5S Lean tool in solving a problem within the terminal.
The activity saw a collaboration of employees from different departments giving a much-needed facelift to the welding section of the Asset Maintenance Department.
Reflecting on what has been learnt through the training program,
Mr. Isaac Acheampong, A Vessel Supervisor said “My takeaway is when you are organized with 5S you work faster and easier. You know where it(work tool) is, and you get it when you need it. You work clean and safer. When organized, your work area – desk/floor is clean, fresh, safe, and beautiful to look at.”
“Some of the key lessons I learned by applying the 5S Lean Management method in the welding area include simplification and visual management. The 5S method encourages simplification and waste reduction by eliminating unnecessary steps, equipment, or materials, resulting in streamlined processes and reduced costs. it also allows the use of visual cues such as labels, signs, and colour coding which help to enhance communication and reduce errors.” Ismail Denwar, a Database Administrator shared.
On his part, Mr. Gabriel Dogbe (QHSSE Officer) added that “for me, it was an awesome experience gained and having been part of the 5S Kaizen in MPS welding shop has really caused me to have a different perspective of how I can be productive, efficient, and safe always both at my workplace and home with the application of 5S in my environment. This is a great tool I recommend for everyone.”
For the welders, it was a welcome change to streamline their work processes and have an improved working environment.
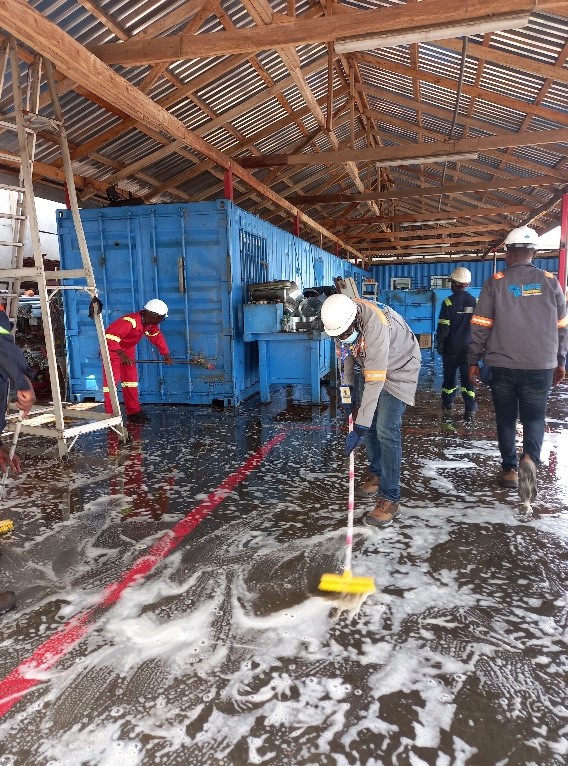

“The Chief Operations Officer, Mr. Curtiss Dakpogan who went round the welding workshop following the work done, stressed the need for sustainability. “I frequent this side of the Workshop often and I must say that there has been some transformation. I believe that sustaining this will be the next step to take it further.”
Commenting on the activity, the Chief Executive Officer of MPS, Mr. Mohamed Samara who has always advocated for the highest level of teamwork amongst staff to achieve the vision of the company remarked. “We are starting to see the result around the terminal where employees implement Kaizens to improve their processes and the way they perform their daily work. Congratulations for the good work done. We are all part of the overall transformation of the Tema Port”.
In the 4-day session, the 6 participants went through the practicality of the 5S lean tool and dwelt on components such as Teamwork, Change Management, Efficient management of the workflow process which was climaxed with the Kaizen event. So far 81% of the MPS staff have received some level of training in Lean practices.

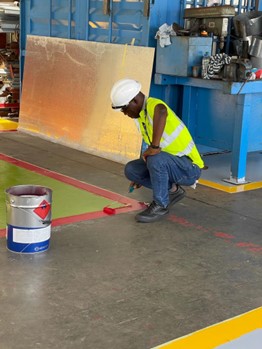
LEAN 5S
The 5S is a problem-solving tool that can help to improve efficiency, productivity, safety, and morale through the following 5 steps.
Sort: Separating of the essential from the nonessential items.
Set in order: Organizing the essential materials where everything has its place.
Shine: Cleaning the work area.
Standardise: Establishing a system to be followed.
Sustain: Ensuring that the system becomes a habit.

MPS has since the onset, believed in continuous improvement, it has pioneered within the port community long-standing best practices and procedures, HSSE standards as well as innovation in handling machinery, technology and operational processes that have given a global facelift to the Tema Port.
With a changed mindset and approach, lean practitioners are expected to take the lead in proposing innovative solutions in the terminal with the goal of improving efficiency and customer service.
No Comments